CASE STUDY
Virtual U.S. Biopharma company sees overall improvement in Quality Culture and ensured uninterrupted supply of compliant DS
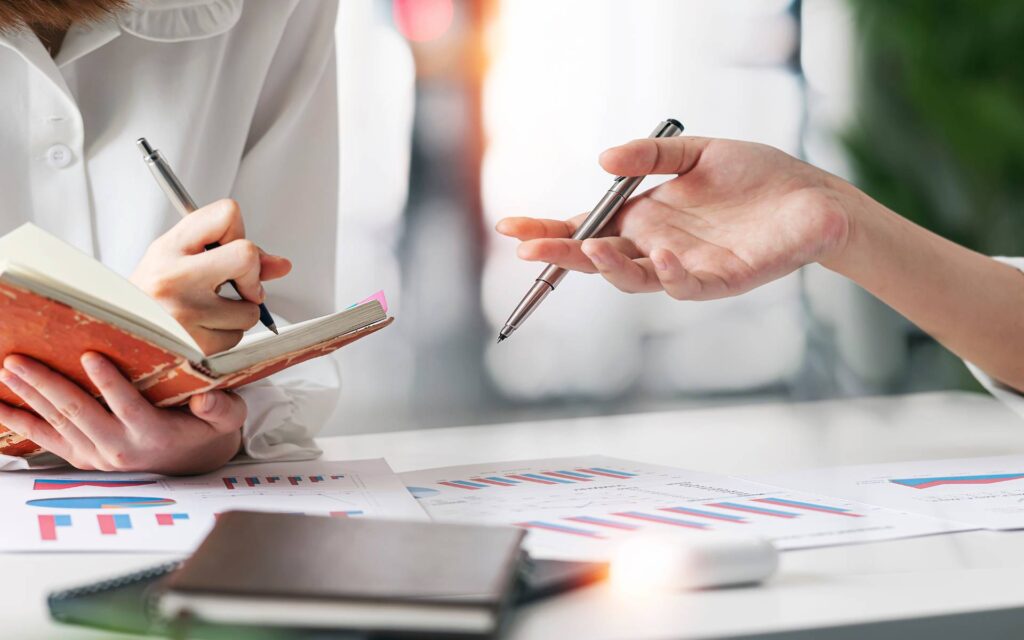
Challenge
Syner-G was contracted by a virtual U.S. Biopharma company to perform the responsibilities of their Quality Assurance function, locally in India. Syner-G Team was vested with responsibility (Quality and Compliance) of two CDMO sites in India for the manufacture of Drug Substance. The legacy contract continued after takeover of the product portfolio by a Big Pharma.
Solution
QA resources (Person-in-Plant – 2 resources) were expected to ensure quality and compliance for drug substance in the Phase III clinical trial. Release of intermediate and DS batches, witnessing critical activities, tracking of QMS activities related to DS, periodic audits such as facility audits, surveillance audits, pre-inspection audits and support of Mock/QP/Supplier Qualification/Regulatory audits were also part of the assignment. The assignment continued for commercial batches after the DP entered market.
Results
Syner-G reviewed a wide spectrum of documents to ensure compliance with respect to GMP requirements. The review of the documents included master and executed batch manufacturing records, batch related deviations, investigations, analytical data, validation reports and protocols. Improvements on procedures were suggested by Syner-G experts to meet the quality and regulatory expectations. The deficiencies in documentation were presented to the CMO and subsequent discussions, onsite visits, mock audits, etc. were held to address the identified concerns and remedial measures were suggested. Quality improvement plans were suggested to vendor sites as appropriate, trainings and workshops were conducted, and examples suggesting current Good Documentation Practices were presented to the stakeholders.
Significant improvement was observed. Procedures, and processes were harmonized and streamlined across all vendor sites. Regular weekly/biweekly discussions with the teams, onsite visits, brainstorming discussions, and quality matrix reviews were part of the activities. Syner-G experts were actively involved in several mock audits, pre-inspection audits and supported QP/Regulatory audits. A robust reporting system with the client was established which involved regular updates, quality matrix, virtual meetings, and a few in-person meetings.
- Ensured uninterrupted supply of compliant DS for the past 20 months (without any single rejection)
- Procedures were harmonised, procedure vs practise was streamlined
- CDMO sites are kept inspection ready and there is an overall improvement in Quality Culture